
Safety Considerations When Using Induction Heating for Welding
Induction heating for welding is a popular technique that can be used to join metal components together. It involves the use of an induction coil, which generates an electromagnetic field and induces heat in the metals being welded. While this method holds many advantages, there are certain safety considerations that must be taken into account when using it. Firstly, it's important to ensure proper insulation of all equipment involved in the welding process. Failure to do so could result in electrical shock or burns (especially when working with higher currents). Additionally, using any kind of flammable material near the welding area should strictly be avoided! The intense heat generated by induction welding may cause such materials to ignite suddenly. Moreover, care should also be taken not to overheat the workpiece(s). This can degrade their structural integrity and even lead to fire hazards. Furthermore, due to its high temperature, induction welding produces hazardous fumes and gases like nitrogen dioxide and ozone that must be adequately ventilated from the workspace. Finally, wearing protective gear such as goggles and gloves is essential for avoiding any injury while working with this method. Conclusively, induction
read more
Uncover the Secrets of Induction Heating for Quicker, Quality Welds
Induction heating is a process that can revolutionize welding! It uses an electromagnetic field to heat metal parts, enabling welders to work faster and with higher quality. This technology has been around for a while but it's often overlooked in favor of traditional methods. But by uncovering the secrets of induction heating, welders can take advantage of its many benefits. First, induction heating speeds up work significantly. Instead of waiting for the material to heat up manually, the electromagnetic field heats it quickly and evenly, saving precious time and energy. Secondly, it prevents warping or distortion due to overheating, resulting in superior-quality welds every time. Finally, this method is cost-effective as it requires less gas and electricity than other approaches. Nevertheless, there are some downsides that must be considered before using induction heating for welding projects. For instance: controlling the temperature accurately can be difficult; more expensive equipment is required; and safety regulations must be followed carefully when dealing with high currents and voltages! Yet if all these potential issues are addressed appropriately then inductive heating can definitely become a game-changer for any professional welder. In conclusion, induction heating offers several
read more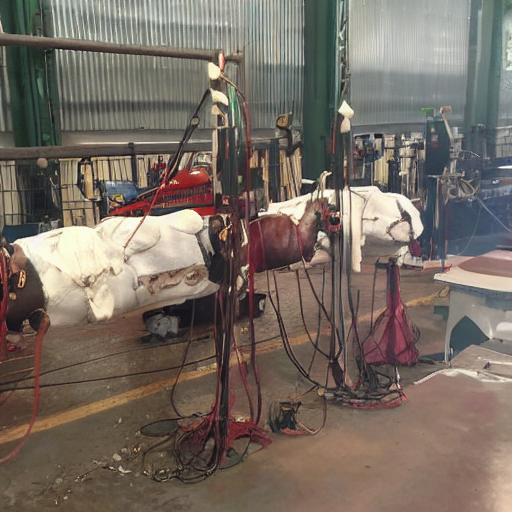
Unlock the Potential of Induction Heating for Your Next Welding Project
Induction heating is a powerful tool for welding projects! It not only provides fast heat-up times, but also offers excellent control over the temperature of the weld. With this kind of precision, it's no wonder why induction heating has become so popular in recent years. But to truly unlock the potential of induction heating for your next project, you'll need to understand how it works and what kinds of advantages it can provide. First off, induction heating works by using electricity to create an electromagnetic field that induces current flow in a metal conductor. The generated eddy currents then produce heat, which quickly warms up the metal part being welded. This process happens almost instantly and enables you to achieve higher welding temperatures than traditional methods like gas or arc welding. Plus, with induction heating there's no risk of combustible materials catching fire. Secondly, one way that induction heating can benefit your welding project is its ability to concentrate heat on specific areas more precisely than other methods. By utilizing different frequencies and intensities you can easily customize the amount of heat applied exactly where needed--greatly reducing distortion and improving overall joint strength!
read more
Additional Benefits for Weld Quality
Induction heat treatment benefits metal heat treatment, induction heating weld preheating, pwht and stress relieving equipment. Easy to install through cable connection panel that does not require removal of sheet metal. Multiple output provides two insulated connectors for air-cooled blankets or liquid-cooled cables. Versatile mobility through a lifting eye or optional running gear designed for construction and maintenance. On-board temperature control provides for manual or temperature-based programming in a simple-to-learn operator interface. Multiple control thermocouple inputs (patent-pending) are available to control on the hottest tc during heating and coolest tc during cooling for uniform heating and quality. Open output detection (patent-pending) prevents system operation without a covered output receptacle (cable or protective plug). When Quality Is Critical Many critical pipe welds completed in the field require preheat to help reduce the risk of cracking and the potential for weld failure. As detailed in d10. 10, several methods are available for jobsite preheating, though some are less efficient and flexible than others. Knowing the pros and cons of each method and choosing the one best suited to a specific application — along with properly applying the heat — can help save time and money and deliver high-quality
read more
Component options for induction heating
Htg induction hardening & induction annealing services what is it? induction heat treating is a process where steel is hardened or annealed by heating, followed by quenching. It is an electromagnetic process using a copper inductor coil, which is fed a current at a specific frequency and power level. Why use induction heat treating / hardening? induction hardening has many benefits such as: localized hardening. Case hardening places a hard case around the entire surface of the part while induction hardening hardens only the precise pattern defined by the inductor coil. The components in the photo above have been cut and etched to show the induction hardened pattern. 25kw high frequency induction welding machine,three phased 380v brazing heating machine this induction heating machine,the device uses a series resonant circuit, low-voltage, high-current, high-frequency power by high frequency transformer output resonance; equipment for our company's first generation products, using mosfet power devices and our first generation variable flow control technology, equipment very simple structure, high reliability, easy maintenance, low maintenance, customer, and is currently the most widely used one of the devices. Features: 1. Under the same conditions, saving a double electric energy than traditional ones. 2. With over-current, over-voltage, under-water, phase failure, load discomfort state, the provision of higher reliability and durability. 3. Applied to the workplace with poor environment, you can put the main host machine in clean space, reducing the host's repair rate, increase the reliability of the device. 4. Can be used in pipeline operations, the small ext machine occupies a small counter top space, easy to move. 5. Design with a 100% load, continuously 24 hours a day, can be equipped with infrared temperature measurement, automatic temperature control, improve the heating quality and simplify the manual operation. High frequency induction heating machine for plastic welding melting the followings are the normal specifications of our 25kw high frequency induction welding machine the result is a dependable custom induction heating system solution that consistently meets your application requirements. 1. Question: generic induction heaters: (one size and design fits all). Is this the case? answer: heating different metals to different temperatures require matching the induction system to the application. Choice of the correct frequency, correct
read more